煤炭作为钢铁生产的主体能源,保障了我国钢铁工业的持续快速发展。然而,在“双碳“目标下,钢铁产业的节能减碳倍受关注。由我校钢铁冶金新技术国家重点实验室郭占成教授负责、国内19家单位联合承担的2016年十三五首批重点研发项目”化工冶金流程工业系统优化与节能技术“取得了重要成绩,日前《科技日报》刊文《流程系统优化让工业生产节能减排》简要介绍了该项目成果。
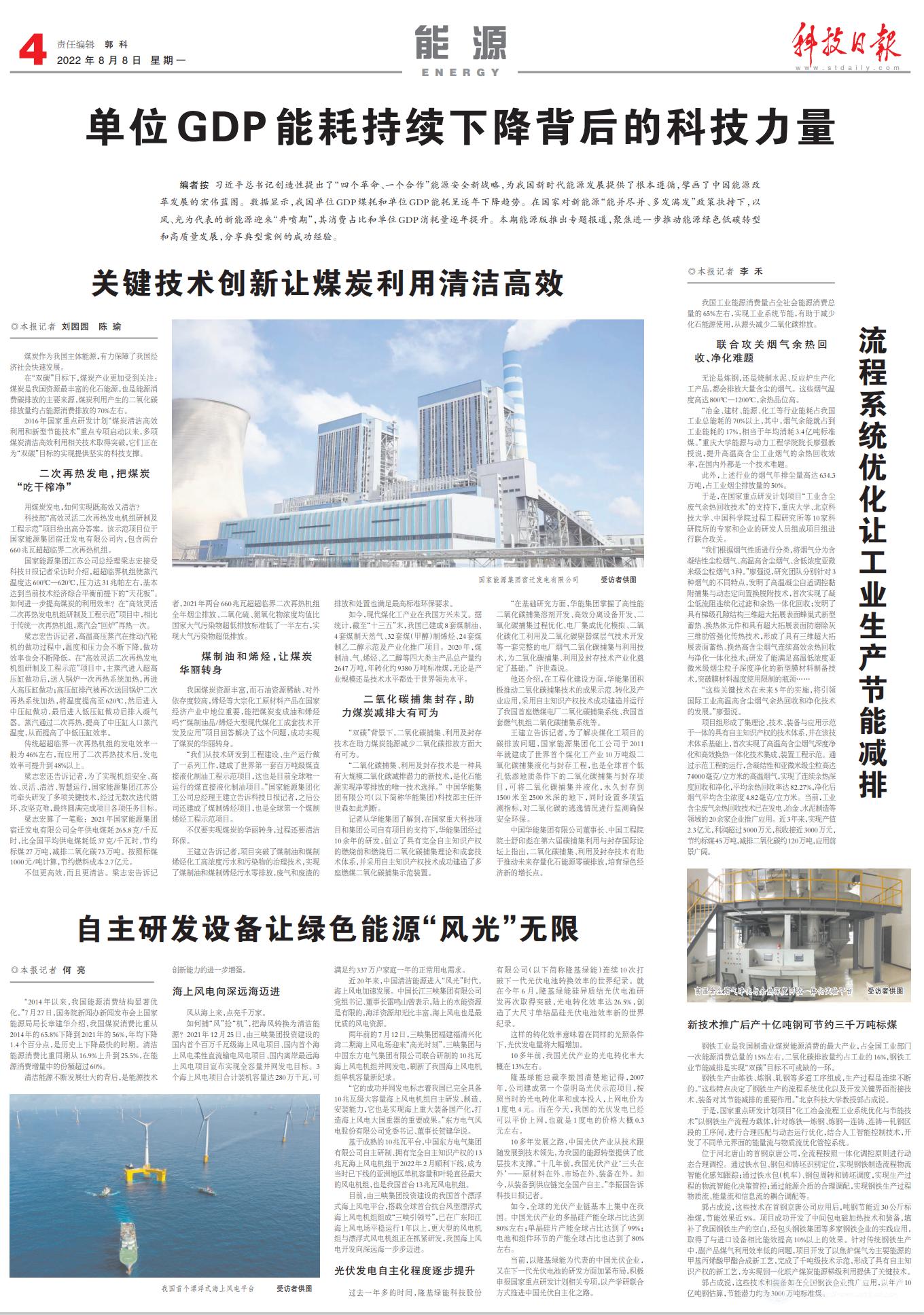
《科技日报》刊文
钢铁生产由焦化、烧结、炼铁、炼钢、轧钢等多道工序组成,生产过程呈连续半连续特点,这一特点决定了钢铁生产的流程系统优化以及开发关键界面衔接技术、装备对其节能减排的重要作用。以我校徐安军教授为主的研发团队,进行工序合理匹配与动态运行优化,结合人工智能控制技术,开发了不同单元界面的能量流与物质流优化管控系统。该系统按照全流程一体化调控原则进行动态合理调控,通过铁水包、钢包和铸坯识别定位,实现了钢铁制造流程物流智能化感知跟踪和生产过程的物流智能化决策管控;通过能源介质的合理调配,实现了钢铁生产过程物质流、能量流和信息流的耦合调配。在首钢京唐公司的大力支持下实现了上线应用,取得了吨钢节能近30公斤标准煤,节能效果近5%的好成绩,这一成果也是冶金流程工程学新领域在实际生产过程应用的突破。此外,项目还成功开发了中间包电磁加热技术和装备,填补了我国钢铁生产的空白,经包头钢铁集团等多家钢铁企业的实践应用,取得了与进口设备相比能效提高10%以上的效果。针对传统钢铁生产中,副产品煤气利用效率低的问题,项目开发了以焦炉煤气为主要能源的甲基丙烯酸甲酯合成新工艺,完成了千吨级技术示范,形成了具有自主知识产权的新工艺,为实现钢—化联产煤炭能源梯级利用提供了关键技术。这些技术和装备如在全国钢铁企业推广应用,以年产10亿吨钢估算,节能潜力可达3000万吨标准煤。
(供图:冶金学院)
(责编:付云笛、邢华超)