近年来,由北科工研研发的冷轧智能工艺模型及大数据分析系统已于鞍钢、马钢、攀钢西昌在内的多家钢铁企业上线并投入使用。该系统面向冷轧精品板材生产,上线后均实现了项目预期效果,各项技术指标达到业内领先水平,标志着北科工研在冷轧智能化方向取得了新的技术突破。
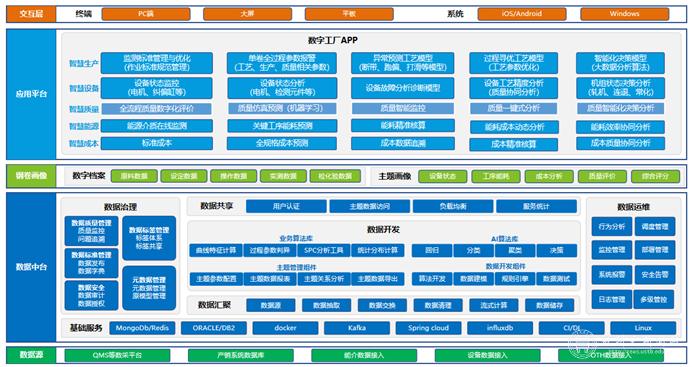
冷轧智能工艺模型及大数据分析系统架构图
在该项技术研发过程中,北科工研以行业数字化需求为导向,凭借多年来在冷轧工艺及质量领域科研攻关项目的技术沉淀,依托工业互联网、大数据、机理模型、AI算法等先进理念和方法,成功开发出覆盖生产、质量、设备、能源、成本5个业务板块的冷轧产线“工业大脑”——冷轧智能工艺模型及大数据分析系统,提高产线的自感知、自诊断、自优化能力,帮助企业提质、增效、降本,实现质量变革、效率变革和模式变革。
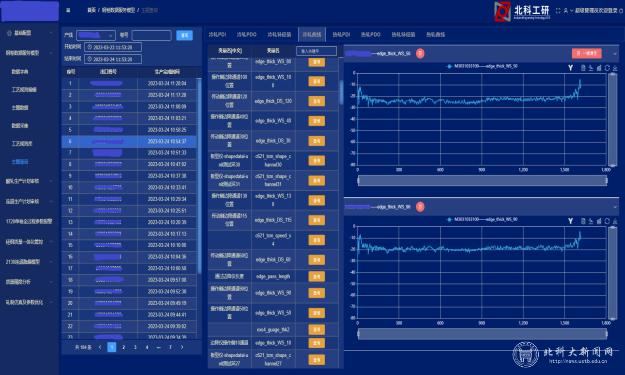
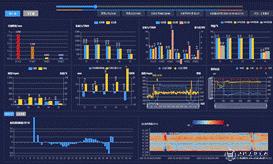
工序间协同分析优化
在提高产量方面,该系统基于专家先验知识,结合各种工业大数据技术和机器学习算法,围绕影响生产稳定性的各类因素,打通“热轧-冷轧-连退”信息壁垒,系统自动进行原料诊断、异常预测、过程寻优、工序间协同优化,大幅提高了生产效率。某现场应用后,通过优化热轧供料标准、给出设备调整建议,酸轧跑偏卷数降低了40%以上;通过原料诊断、优化冷轧轧制参数,轧制断带率降低了40%以上;通过大数据分析反向优化冷轧板形,连退跑偏卷数降低60%以上。
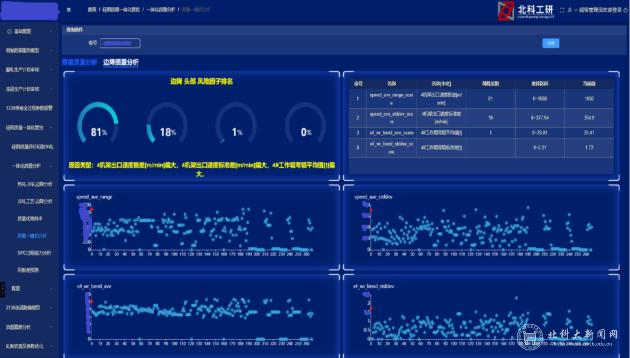
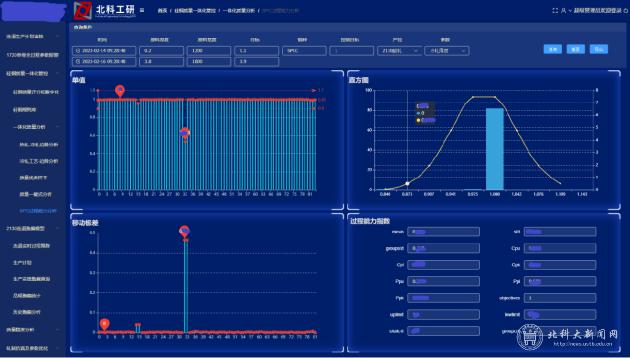
质量协同分析优化
在产品质量控制方面,该系统基于全流程过程数据的精准映射与挖掘分析,结合冷轧机理模型和知识规则,开发了质量数字化评价、质量仿真预测、质量智能监控、质量一键式分析(质量、设备精度、工艺窗口协同分析)等相关模块,实现了质量一贯制管理。现场应用后,通过质量精准管理、工艺窗口实时监控等手段,产品性能稳定性及硅钢同板差控制精度大幅改善,废次降比例降低了0.2%以上。
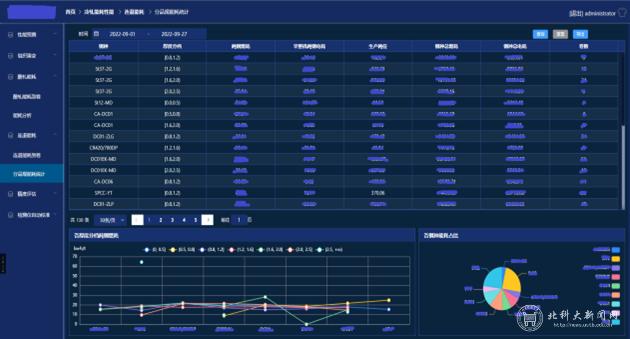

能源精细化分析
在降本节能方面,该系统针对钢铁企业降本增效减排的迫切要求,开发了产线能源精细化管控和成本精准核算分析等模型功能,通过能源成本协同优化,降低产线吨钢能源消耗和生产成本。某厂应用后,通过优化冷轧加宽量和热轧供料宽度,吨钢成本降低约1元/吨。
(供图:工研院)
(责编:付云笛)