基于在钢铁、有色全流程质量管控系统方面的深刻认知及丰富的实施经验,北科工研针对单条产线定制化开发的单工序质量管控系统同样也给多个炼钢、连铸、热轧、冷轧工厂带来了“小系统,大作用”的切身体会。
近期,由攀钢集团科技管理部、攀钢研究院、攀钢西昌钢钒科技质量部、攀钢西昌钢钒板材厂组成的专家组对北京科技大学工程技术研究院(北科工研)承担的《自由轧制中板带质量改进技术》项目进行评审验收。北科工研项目组对项目实施内容、成果进行了系统汇报,专家组经过询问、讨论后,一致同意该项目通过考核验收,并对北科工研取得的成果给予了肯定。在此项目中,北科工研搭建的热轧过程质量管控系统发挥了显著作用。
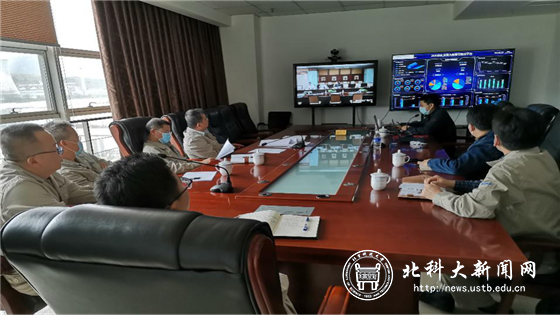
自由轧制是各热轧企业不断追求的目标,也是众多单项技术的集成,如辊形技术、模型技术、装备技术、工艺技术等,可有效打破热轧计划编排约束,这对于增加铸轧之间的柔性、提高热装热送比例、降低非计划材、及时响应市场需求等均具有积极的意义。但事实上,对于产线单一而品种规格众多的企业,由于无足量、合适的烫辊材、过渡材,面对自由轧制,不是“能不能”的问题,而是必须适应。由于自由轧制放宽了计划排列对钢种、宽度、厚度变化的约束,容易导致模型、设备、工艺条件的适应能力下降,不可避免会造成轧制过程的不稳定性及质量偏差。本项目聚焦如何基于现有的设备能力及模型鲁棒性对轧制有效自由度进行评估、优化,并发现短板,最大限度保证生产、质量稳定前提下逐步提升轧制自由度。热轧过程质量管控系统的搭建则给本项目的实施提供了完整的数据、算法支撑,并形成了一批定制化解决方案。本项目的研究思路是构建在线精准的质量过程判定系统,并将质量判定结果与计划、模型、工艺等进行关联,通过数据挖掘的方法找出自由度提升的短板,并进行改进、优化,不断提升频繁换规格过程中的产品质量。
项目通过封装智能工艺网关,形成具有行业特色的边缘侧数据处理技术,突破工艺对象过程原理不明确的瓶颈,实现了工艺数据的时空变换、匹配、判异等功能。以此为基础,构建了面向热轧多区域、多系统的数据平台,完成了以物料为中心的高通量、多源异构、多维度数据采集,得到热轧数字钢卷。平台构建完成后数据可靠性达到100%,多区域、多主题、多粒度质量数据追溯时间小于1s,为自由度与生产、计划、质量的关联分析提供了基础条件。
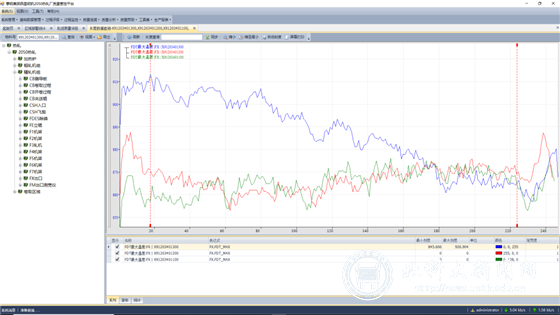
以热轧数据平台为基础,形成具有热轧特色的多类模型库和算法库,开发了涵盖过程判定、过程监控、数据追溯、质量分析、质量预测、质量协同的多模块工艺质量管控智能应用,形成了热轧工艺质量管控的新模式,实现了产品质量的事后判定与评价、事中监控与预警、事前预测与管控、质量缺陷分析与追溯、多要素质量协同控制等功能,为热轧频繁换规格轧制时的产品质量保驾护航。
项目开发的过程判钢融合了表达式引擎、规则模糊化、缺陷识别等多种技术,尺寸、温度、板形类判定准确率接近100%,这一结果同时也解决了人工水平差异造成的误判、漏判,精准的过程质量判定结果不但是轧制计划评价、优化的输入条件,也在质检减员、完善现有MES系统判钢方面起到了积极的作用;实时监控诊断预警功能将“事后监控”转化为“事中控制”,避免了提升轧制自由度造成的轧制过程不稳定和批量质量偏差,如通过操作台实时监控预警功能,及时发现了不同品种、不同规格侧导板压力与带钢边部刮伤的关系,使得边部刮伤缺陷下降72%;多维数据追溯技术实现了各个业务系统数据贯通与共享,自由轧制换规格缺陷原因查找效率提升30%以上;通过质量缺陷分析,实现了换规格质量问题的精准定位和辅助决策,如明确了层冷换热系数在不同的厚度规格切换时的合理区间,宽度补偿系数对换规格宽展量的影响等。
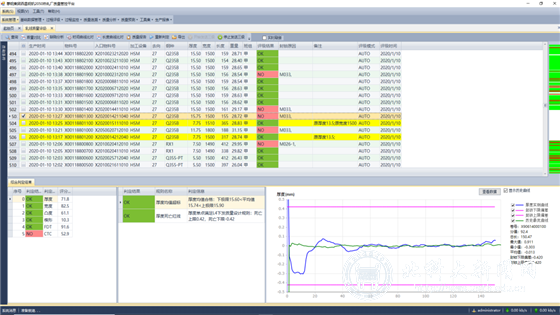
攀钢西昌热轧过程质量管控系统成功实施以来,自由轧制换规格综合质量封闭率下降22.29%,在提升自由度轧制的同时保障了其产品质量的稳定性,进而为企业带来经济效益,实现提效创效,
攀钢2050mm热连轧工艺质量管控系统的成功实施与应用,验证单工序质量平台在解决工厂级问题的优势和定制化能力,其相关技术目前也正在宝武梅钢热轧、梅钢冷轧、吉林建龙热轧、日照钢铁公司冷轧等多个工厂得到应用, 促进了钢铁工业的工厂级智能化进程和技术革新。
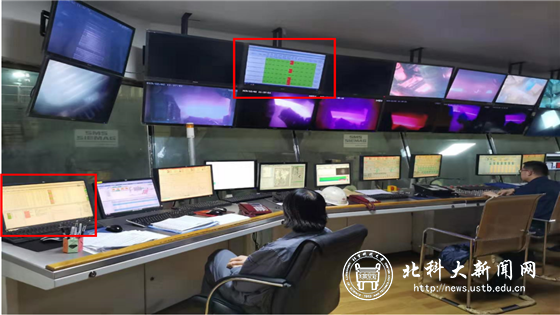
(图片:工研院)
(责编:付云笛)